インジェクション成型とは?射出成型の仕組み・工程・主な種類5つ
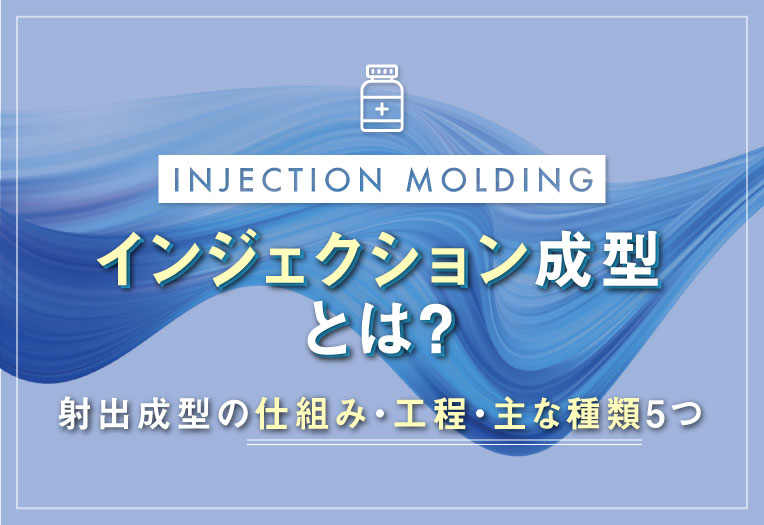
樹脂(プラスチック)には熱によって変質するという特性があるため、樹脂を加熱することによって金型を使用した成型などの加工が行えます。樹脂加工で使用される成型技術の一つが、インジェクション成型です。
インジェクション成型は成型加工のスピードが早く、複雑な形状の成型もできます。大量生産に適した加工法であるため、身の回りにもインジェクション成型で作られた製品を見つけられるでしょう。
今回は、インジェクション成型の特徴や用途・仕組み、インジェクション成型以外の成型方法について解説します。
1.インジェクション成型とは?
インジェクション成型とは、原料を熱で溶かして流動性を持たせ、金型内に高圧で射出し、冷却・固化することによって成型する加工法です。インジェクションは日本語で「射出」の意味であり、射出成型とも呼ばれます。
樹脂加工におけるインジェクション成型では、原料としてプラスチックペレットを使用します。プラスチックペレットとは、熱で溶融しやすいように粒状になったプラスチック樹脂のことです。熱で軟化した樹脂は金型で容易に成型できるため、インジェクション成型は最もポピュラーな樹脂の成型加工方法と言えます。
また、インジェクション成型には以下のようなメリットがあることから、製品の大量生産に適した方法です。
- 成型の精密性が高い
- 金型の形状に沿った複雑な成型ができる
- 金型を一度製作すれば連続的に短時間の生産が可能
1-1.インジェクション成型の用途
インジェクション成型の用途は広く、以下のように工業用部品・自動車部品から、電子機器・医療用品・理化学機器、玩具・日用品まで使用されています。
- 工業用の小型ギア、ワッシャー
- 自動車のドアピラー、バンパー
- ノートパソコンの筐体
- 電子機器のコネクタ
- 医療用トレイ、注射器
- ピペット先端部やサンプル容器
- コンテナ
- ホース継手
- 化粧品容器
- プラモデルなどの玩具
- 歯ブラシ、洗面器、収納ケースなどの日用品
など
また、樹脂ボトルの場合、キャップをインジェクション成型で製造していることが特徴です。容器本体は、樹脂を金型内で膨らませるブロー成型によってボトル状に成型しています。
1-2.インジェクション成型の仕組み・流れ
インジェクション成型では、射出成型機と呼ばれる専用の機械を使用します。プラスチックペレットの準備から、成型品を取り出すまでの一連の流れを見てみましょう。
(1)材料の準備 |
---|
プラスチックペレットを射出成型機のホッパーへ投入します。投入されたプラスチックペレットはシリンダーに送られ、バンドヒーターで加熱されて水あめ状に溶かされます。射出ユニット内のスクリューによりプラスチックペレットが圧縮混練され、シリンダー前方へ送られることで材料の準備は完了です。 |
(2)型締め |
---|
金型の固定側ダイプレート・可動側ダイプレートを閉じ、射出あとに動かないように締め付けます。 |
(3)射出 |
---|
溶けたプラスチック樹脂を、シリンダーの先端から金型へと射出・充填します。 |
(4)保圧 |
---|
金型へ射出したプラスチック樹脂に一定の圧力をかけます。溶融したプラスチック樹脂がシリンダーへ逆流することを防ぐとともに、冷却過程における収縮現象を防ぐための工程です。 |
(5)冷却 |
---|
金型を冷却水またはオイルで冷却し、金型内のプラスチック樹脂を固化させます。冷却時間が長いと成型サイクルが伸びて生産性は悪くなるものの、短すぎると収縮が発生しやすくなるため、インジェクション成型の成功を左右する重要な工程です。 |
(6)型開き |
---|
金型内のプラスチック樹脂が十分に固化したら、成型品を取り出すために金型を開きます。成型品は金型の可動側ダイプレートに付いています。 |
(7)取り出し |
---|
金型を開いたあとは、可動側ダイプレートに付属しているエジェクターピンで成型品の突き出しを行います。金型から外れた成型品を回収することで取り出しは完了です。 |
以上が、樹脂加工におけるインジェクション成型の1サイクルです。インジェクション成型のサイクルを繰り返すことで、樹脂製品を大量生産できます。
2.インジェクション成型以外に知っておくべき「成型方法」5つ
プラスチック樹脂は、熱可塑性樹脂と熱硬化性樹脂に大別されます。それぞれ以下のような性質を持ちます。
熱可塑性樹脂 | 加熱すると溶融して液体化し、冷却すると硬化して固体化する |
---|---|
熱硬化性樹脂 | 液体から加熱すると硬化し、硬化後は加熱・冷却しても液体に戻らない |
このように、熱可塑性樹脂と熱硬化性樹脂は性質が異なるため、素材に応じた成型方法を選択することが大切です。以下では、インジェクション成型以外の代表的な射出成型方法を5つ紹介します。
2-1.ガスアシスト射出成型
ガスアシスト射出成型とは、射出成型の保圧工程においてプラスチック樹脂に不活性ガスを注入し、中空構造の成型品を作る成型方法です。高圧のガスが樹脂内部から均一に圧力をかけることで、樹脂ボトルや樹脂パイプを作成できます。
●ガスアシスト射出成型の特徴とメリット
- 肉厚が均一な中空構造の成型品を得られる
- 成型品のヒケ(へこみ)やソリを防止できる
- 原料である樹脂の使用量を抑えられる
中空構造にすると製品形状を保ったまま重量を減らせるため、ガスアシスト射出成型は軽量化技術としても利用されています。
2-2.二色成型
二色成型とは、異なる色の同種樹脂、または異なる種類の樹脂材料同士を組み合わせて一体化させる成型方法です。2種類の材料は成型工程で溶着されるため、後工程で接着する必要はありません。
●二色成型の特徴とメリット
- 2つの樹脂材料を組み合わせることで、見た目や性能に付加価値が生まれる
- 後工程でパーツ接着・組み立てなどが不要であり、コスト削減ができる
二色成型を選択するときは、組み合わせる材料の相性を考慮することが重要です。組み合わせる材料同士に親和性があり、温度変化の性質も同一などでなければ、二色成型は成功しません。
2-3.低圧成型
低圧成型とは、シリンダー内の樹脂を金型へ射出するときに、樹脂を押し出すスクリューの射出圧力を低く設定する成型方法です。
●低圧成型の特徴とメリット
- 成型品のガス焼けやバリ・変形を防げる
- 型締力の小さい成型機で成型を行える
ガス焼けとは、樹脂を高速射出した際に金型内のエアベントから空気が十分に排気されず、断熱圧縮で高温となった空気に樹脂が触れて焼けることです。低圧成型は樹脂を低圧で射出するため、成型品のガス焼けを防ぐことが可能です。
2-4.射出圧縮成型
射出圧縮成型とは、金型を少し開いた状態で樹脂を射出したあとに、金型を型締めして圧縮する成型方法です。射出部に圧力が集中するインジェクション成型に対し、射出圧縮成型では圧力を均一に分散できるという特徴があります。
●射出圧縮成型の特徴とメリット
- 残留ひずみやヒケなど、成型品の成型不良を防げる
- ランナー部のバリを防げる
- 肉厚の薄い成型品を作れる
射出圧縮成型では、金型で圧縮することで成型形状を得るため、金型設計時の寸法測定や型締力には高い精度が求められます。成型に使用する射出装置も特殊となり、コストがかかることは注意点です。
2-5.インモールド成型
インモールド成型とは、装飾用デザインを印刷したベースフィルムを金型内に挿入してから樹脂を射出することで、樹脂表面にフィルムのデザインを転写する成型方法です。
●インモールド成型の特徴とメリット
- 成型後の外観塗装工程を削減できる
- 樹脂表面に転写されるため、複雑な形状にも対応できる
- 成型工程で成型品にハードコート処理が行える
インモールド成型で得られた成型品は、すでに加飾された状態になります。そのため、成型品がそのまま完成品となるプラスチック製品であれば、仕上げ加工にかかるコストを削減することが可能です。