半導体製造の後工程とは?フローや後工程の重要性を解説
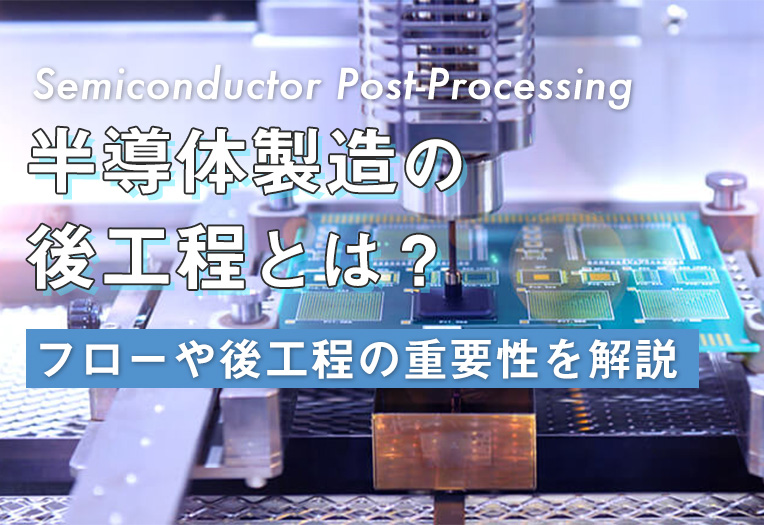
自動車や家電製品には、すべて半導体が使用されています。日常生活で当たり前のように触れるスマートフォンやパソコンにはもちろん、近年ではIoT機器や医療機器にも広く活用されており、半導体は現代社会に欠かせない存在と言えるでしょう。
半導体製造工程には大きく「設計」「前工程」「後工程」の3つがあり、異なる役割をもつ各プロセスを経て精密な回路が形成された後、さまざまな製品に組み込まれます。
そこで今回は、半導体の性能や耐久性を左右する後工程の具体的なフローや重要性について詳しく紹介します。
1.半導体とは?
半導体とは、電気を通す「導体」と、電気を通さない「絶縁体」の両方の性質を兼ね揃えた物質のことです。
導体には金属や水が挙げられ、電気をよく通すことが特徴であるのに対し、ゴムやプラスチックといった絶縁体は基本的に電気を通しません。
半導体はこの導体と絶縁体の中間の性質をもっており、電気や磁場を加えることで「電気を通す・通さない」を瞬時に切り替えられます。
半導体の主な材料としては、自然界に豊富に存在し、加工しやすい特性を有した「シリコン」が広く利用されています。しかし、「半導体」という言葉は単なる物質を指すのではなく、半導体を材料に用いたトランジスタや集積回路全体などのデバイス全体も慣用的に半導体と呼ばれています。
半導体の発見と技術革新によって、電子機器の小型化・高性能化が急速に進みました。現在では、家電製品や自動車のほか、スマートフォン・パソコン、産業機器、医療機器、通信インフラなど、さまざまな分野の電子部品で半導体が不可欠な存在となっています。
2.半導体の製造工程
半導体を製造する工程には、大きく分けて「設計」「前工程」「後工程」の3つがあり、それぞれ異なる役割をもっていることが特徴です。これらのプロセスを経て精密な回路が形成され、最終的にさまざまな製品に組み込まれます。
ここからは、半導体の各製造過程の概要を説明します。
2-1.設計
ものづくりは設計から始まるのが基本であり、当然半導体も例外ではありません。半導体の設計工程では、まず仕様に基づいた回路・パターンを設計した後、フォトマスクを作成します。
●回路・パターン設計
半導体のICチップ上にどのような回路を配置するのかをあらかじめ設計し、シミュレーションを重ねて最も効率的なパターンを検討します。用途によって必要な機能は異なるため、設計パターンも都度異なることが基本です。
●フォトマスク作成
コンピューターを使って、透明なガラス板の表面に設計した回路パターンを大きく描きます。このガラス板は、次の工程でつくるシリコンウェーハに設計回路を転写するための原版(マスタ)となります。
2-2.前工程
半導体製造における「前工程」は、シリコンウェーハの基盤上にトランジスタなどを含む電子回路を高集積で形成して半導体チップの基盤をつくる工程です。下記のように、多くの作業が存在します。
- ウェーハの生成
- ウェーハの研磨
- ウェーハの酸化
- ウェーハ表面への薄膜形成
- ウェーハ表面へのパターン転写
- ウェーハ表面のエッチング
まずはワイヤーソーと呼ばれる機械を用いて、超高純度に生成されたシリコンの単結晶インゴットを薄くスライスし、ウェーハをつくります。インゴットを薄く切断してつくったウェーハ表面には、細かな凹凸があります。ウェーハが鏡状になっていなければ、回路パターンの品質が保てません。そのため、研磨剤や研磨パッドを用いて鏡面状に磨きます。
その後、ウェーハに回路パターンを焼き付けるため、高温の拡散炉にさらしてウェーハ表面に酸化膜をつけます。酸化膜をつけたらフォトレジストを薄く均一に塗布し、フォトマスクを通してウェーハ表面に回路パターンを転写します。
回路パターンを焼き付けたら、ウェーハ表面のエッチングを行い、フォトレジストのない部分の酸化膜と不要となったフォトレジストを除去します。
2-3.後工程
半導体製造における「後工程」は、ウェーハから繊細な半導体チップを切り出して各種パッケージに封入する工程です。大きく「組立工程(パッケージング工程)」と「検査工程(テスト工程)」の2段階に分けられます。
組立工程 |
|
---|---|
検査工程 | 検査・試験 |
後工程は、半導体チップを完成品へと仕上げる重要なプロセスです。特に組立工程は、ウェーハからチップを切り出して基板やリードフレームへ実装するなど、複数の作業が含まれます。一方の検査工程では、完成した半導体の性能を確認しつつ、不良品を排除するために行われることが特徴です。
3.半導体製造の後工程のフローを解説
半導体製造における後工程には、ダイシング(半導体チップの切り出し)からモールディング(強度の向上)、さらに実際の使用環境に基づく最終検査までと、複数の作業が必要です。
ここからは、半導体製造の後工程の各フローについて詳しく説明します。
3-1.ダイシング
ダイシングとは、前工程でつくられた薄い円板の半導体ウェーハをダイヤモンドプレートで四角く切り出し、個別のチップとして分割する工程です。
ダイシングでは、「ダイサー」と呼ばれる半導体製造装置を用いてウェーハを精密に切断します。切断面に欠けやクラック(ひび割れ・亀裂)があると半導体製品の品質に大きな影響を及ぼすため、慎重な操作が必要です。ウェーハの薄化が進む近年では、切断時の振動や応力を最小限に抑えられる技術も誕生しつつあります。
なお、ダイシングを行った後は切断面の仕上がりをチェックします。チップとして使われるのは、破損が見られない良品のみです。
3-2.マウンティング
マウンティングとは、ダイシングで切り出された個別のチップをリードフレーム(基盤)の所定の位置に配置する工程です。配置の際は、基本的に「フリップチップ技術」または「リフローマウンティング技術」が用いられます。
●フリップチップ技術
チップを逆さまにしてリードフレームに直接接合する方法です。配線が短くなるため、電気信号の伝送速度が高まるほか、高密度・高速な接続が可能となります。
●リフローマウンティング技術
チップをリードフレームに配置した後、ハンダを溶かして接合する方法です。一度に複数のチップを接合できるので、大量生産にも適しています。
マウンティングのプロセスで最も重要なのが、安定した接合の確保です。接合時のわずかなズレは製品の性能に大きな影響を及ぼすため、細心の注意を払って作業を進める必要があります。
3-3.ワイヤーボンディング
ワイヤーボンディングとは、チップとリードフレームを「ボンディングワイヤー」と呼ばれる約25μmの金属製ワイヤーで接続する工程です。ワイヤーボンディングを行うことで、電気的な接続が確保され、信号の伝達が可能となります。
ワイヤーボンディングのプロセスで重要となるのが、接続点の精度です。接続時のわずかなズレはチップの動作不良につながるため、高度な技術が求められることを覚えておきましょう。
3-4.モールディング
モールディングとは、ワイヤーボンディングを経たチップを、モールド樹脂やセラミックでパッケージングして保護する工程です。チップ全体を保護することによって、外部からの衝撃はもちろん温度や湿度の変化からも守れます。
モールディングに使用する素材は製品の用途によって異なるので、適切な半導体材料の選定とプロセスの管理が必要です。加えて、モールディングの際はチップに均一に塗布するための高度な技術が求められることも覚えておきましょう。
3-5.検査・試験
ダイシングからモールディングまでの組立工程が終わったら、半導体検査装置を用い、検査工程で完成したチップが設計通りに機能するかを確認します。最終検査では、各チップが正常に動作するか・設計書通りの電気的特性であるかを確認するためのテストだけでなく、外観検査も行われます。
厳格な基準に基づき品質が評価されたチップのうち、一定の基準をクリアしたチップのみが製品として市場に出荷されます。この段階で不良が見つかったチップは取り除かれます。
また、最終検査で得られたデータは生産工程全体のフィードバックとしても活用可能です。不具合傾向や発生原因を分析することで、製造・開発プロセスの改善につながるほか、品質向上にも貢献します。
このように、検査・試験工程は単なる不良品の排除だけでなく、半導体製造プロセス全体の最適化にも重要な役割を果たします。
4.半導体製造の後工程が重要な理由は?
かつて、半導体製造の中心は前工程であると考えられていました。半導体技術の進化は、主に回路の線幅を狭め、集積度を高める「微細化」によって成し遂げられました。この過程で主に関与していたのが前工程であり、微細化においての主戦場となっていました。
しかし現在では、回路の線幅は極小化され、物理的な制約やコストの問題が顕在化したことによって、微細化の限界に近づきつつあるとされています。
新しい技術への転換が求められる中で注目されたのが、「チップレット技術」の進化です。チップレット技術とは、複数の半導体チップを組み合わせて1つの半導体パッケージに収める次世代技術です。微細化に依存せずより低コストで半導体の性能向上を実現できる可能性があることから、非常に高い期待が寄せられています。
しかし、チップの組み合わせや接続には高精度な技術が必要なため、チップレット技術の成功においては後工程における技術革新が不可欠です。今後は後工程技術の進展がチップレット技術のさらなる実用化と信頼性向上を支え、半導体製造における新たな可能性を切り開くカギとなるでしょう。
まとめ
半導体製造における「後工程」は、前工程でつくられたウェーハから繊細な半導体チップを切り出して各種パッケージに封入する工程です。チップレット技術が発展する近年、後工程は半導体の性能向上やコスト削減に貢献しており、今後の半導体製造技術の革新につながる中心的な役割を果たすことも期待されています。
半導体業界では、さらなる高性能化が求められており、今後の後工程において、日本の技術がますます重要になってくると想定されます。半導体の製造では、特殊な薬液や接着剤が使用されますが、たとえば、接着剤については、光の影響やパーティクル汚染を防止する必要があり、容器もそれらを考慮したものである必要があります。
サンプラテックでは、遮光性に優れた容器をラインナップしております。
また、クリーン洗浄や酸洗浄など、二次加工品の対応も可能です。規格外のご要望にも柔軟に対応しておりますので、遮光瓶の二次加工品についてもお気軽にご相談ください。